dimensioning(Dimensioning)
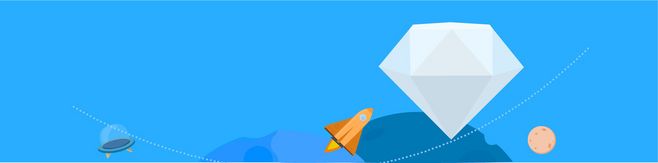
Dimensioning
Introduction to Dimensioning
Dimensioning is an essential process in engineering and design to communicate the size, shape, and location of physical objects. It involves the creation and placement of accurate measurements on technical drawings, ensuring that the design intent is clearly conveyed to manufacturers, builders, and other stakeholders. Dimensioning is critical for achieving accuracy, promoting manufacturing efficiency, and minimizing errors in the manufacturing and assembly process.
The Importance of Dimensioning
Accurate and precise dimensioning is crucial in engineering and design for several reasons:
1. Clarity and Communication: Dimensioning provides clear instructions and information to manufacturers, fabricators, and assemblers, ensuring that the design intent is properly understood. Without accurate dimensions, misinterpretations can occur, resulting in errors, delays, and costly rework.
2. Manufacturing Efficiency: Proper dimensioning enables manufacturers to determine the most effective and efficient methods for producing a specific part or assembly. It aids in selecting appropriate machining processes, tooling, and materials, leading to increased productivity and reduced manufacturing time and costs.
3. Assembly and Fit: Dimensioning plays a crucial role in ensuring that different components of a product fit together well during assembly. By providing accurate measurements, designers can ensure proper alignment, clearance, and functionality of parts, resulting in a well-functioning and reliable final product.
4. Quality Control: Accurate dimensioning is necessary for quality control inspections and evaluations. Dimensions serve as references for measuring and verifying the conformity of the manufactured parts to the original design specifications. Any deviations or variations can be quickly identified and rectified, maintaining high-quality standards.
Basic Principles of Dimensioning
When dimensioning a technical drawing, certain principles should be followed to ensure clarity and consistency:
1. Use Standardized Symbols and Conventions: Unified standards and symbols, such as the ASME Y14.5 standard, should be followed for dimensioning to ensure that the drawings are universally understood by manufacturers and other stakeholders.
2. Clear and Readable Dimensions: Dimensions should be placed clearly and legibly on the drawing, avoiding clutter and overlapping. They should be placed outside the view of the object and spaced appropriately to avoid confusion.
3. Use Different Dimensioning Techniques: Depending on the type of object and the features being dimensioned, different techniques such as linear dimensioning, chain dimensioning, and baseline dimensioning may be used. The appropriate technique should be selected to provide the most accurate and comprehensive information.
4. Dimension to Critical Features: Critical features, such as those affecting function, fit, and assembly, should be dimensioned explicitly and clearly. Non-critical features may be omitted or referenced to key dimensions.
5. Use Tolerances: Tolerances should be specified to define the acceptable variations in dimensions. They ensure that the final product functions and fits within the desired limits and provide guidance for manufacturing and inspection processes.
Conclusion
Dimensioning is a vital aspect of engineering and design that allows for accurate communication and manufacturing of objects. By properly dimensioning technical drawings, engineers and designers can effectively convey their design intent, promote manufacturing efficiency, facilitate proper assembly, and ensure high-quality products. Following standardized dimensioning practices and principles is necessary to ensure clarity, consistency, and universal understanding of the dimensioned drawings. Dimensioning plays a crucial role in achieving precision, accuracy, and successful realization of designs in various industries.