diecasting(Diecasting Technology Delivering Precision and Durability)
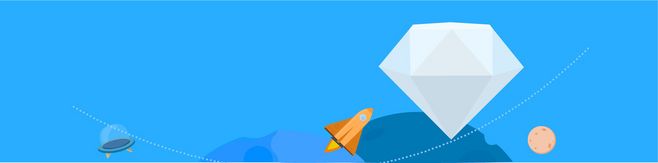
Diecasting Technology: Delivering Precision and Durability
Introduction: Mastering the Art of Diecasting
Diecasting is a highly efficient manufacturing process that has revolutionized the production of complex metal parts. With a history dating back to centuries, diecasting has evolved and perfected over time, enabling the creation of intricate designs with unparalleled precision and durability. This article will delve into the intricacies of the diecasting process, explore its applications across different industries, and shed light on the reasons why diecasting has become the go-to method for producing high-quality metal parts.
The Diecasting Process: Molding Perfection
Diecasting involves injecting molten metal into a die or mold under high pressure, resulting in the formation of a solid metal component. The process begins with the preparation of the die, which is typically made of steel and consists of two halves - the stationary half (called the cover die) and the moving half (called the ejector die). These halves come together to form a cavity that defines the shape of the desired part.
Once the die is ready, the next step is the melting and preparation of the metal alloy. The choice of metal alloy depends on the specific application requirements, with aluminum, zinc, and magnesium being commonly used due to their exceptional properties. The molten metal is poured into a furnace and heated to its optimal temperature before being injected into the die using a high-pressure machine.
During the injection phase, the high pressure ensures that the molten metal completely fills the cavity and takes on the intricate details of the mold. Once the metal solidifies, the die is opened, and the finished component is ejected. This process is highly repeatable and can be automated, making it ideal for high-volume production.
Applications and Advantages: Versatility and Excellence
The versatility of diecasting makes it a preferred choice for a wide range of industries, from automotive and aerospace to electronics and consumer goods. The process allows for the production of complex parts with exceptional dimensional accuracy, thin walls, and intricate features. The ability to produce parts with high precision leads to improved assembly, reduced rework, and enhanced overall product performance.
Diecasting also offers significant cost advantages. The long tool life of the die ensures a high number of parts can be produced before replacement is required, reducing per-unit costs. The fast cycle times and high production rates further contribute to cost-efficiency, making diecasting a viable option for large-scale manufacturing.
Furthermore, diecast parts exhibit excellent mechanical properties, including high strength, hardness, and heat resistance. They are also lightweight compared to alternative manufacturing methods, making them desirable for applications where weight reduction is a critical factor, such as in the automotive industry.
In addition to its technical advantages, diecasting is also environmentally friendly. The recyclability of the metal alloys used in the process contributes to sustainable manufacturing practices. The efficient use of energy and the minimal waste generated during production make diecasting an eco-conscious choice.
Conclusion: Empowering Industries with Diecasting
Diecasting has emerged as a leading technology that delivers precision, durability, and versatility in the manufacturing industry. Its ability to produce complex parts with exceptional accuracy and mechanical properties has revolutionized various sectors. From automotive components to electronic enclosures, diecast parts have become indispensable in enhancing product performance and efficiency. With ongoing advancements and innovations in diecasting technology, this manufacturing process will continue to shape and transform industries for years to come.