dimensioning(Understanding the Concept of Dimensioning in Engineering)
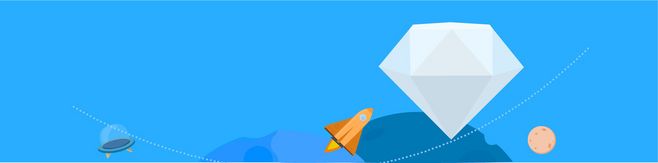
Understanding the Concept of Dimensioning in Engineering
Introduction:
Dimensioning plays a crucial role in engineering design and manufacturing processes. It involves specifying the size, shape, and location of features on an object in accordance with a set of standards. Dimensioning ensures that a product can be accurately manufactured and assembled, and that it meets the functional requirements and tolerances set by the design engineer. This article aims to provide a comprehensive understanding of dimensioning by exploring its principles, techniques, and significance in various engineering disciplines.
Principles of Dimensioning:
Dimensioning is guided by a set of principles that are universally followed in engineering practice:
1. Clarity and Unambiguity:
Dimensioning should be clear, precise, and unambiguous, leaving no room for interpretation. It should communicate the intended size and location of features accurately to those involved in the manufacturing and assembly processes.
2. Datum Reference Frame:
A datum is a theoretical perfect reference line, plane, or point from which dimensions are measured. The use of a datum reference frame establishes a common set of references for dimensioning, ensuring consistency and interoperability.
3. Tolerance and Fit:
Tolerance refers to the allowable variation in a dimension. It is essential to specify tolerances for each dimension based on the functional requirements of the part and the capabilities of the manufacturing process. The fit is the relationship between the parts that are assembled together, and it is defined by the tolerance.
Techniques of Dimensioning:
Several techniques are employed in dimensioning to effectively communicate the design intent and facilitate manufacturing processes:
1. Size Dimensions:
Size dimensions indicate the actual measurements of features, such as length, width, and height. They are typically placed in line with the dimension lines and are expressed in units of measurement.
2. Location Dimensions:
Location dimensions specify the exact position of features relative to a datum or other features. They include coordinates, such as distances from edges or centerlines, angles, and arcs. Location dimensions are critical in ensuring proper alignment and fit of the components.
3. Geometric Dimensioning and Tolerancing (GD&T):
GD&T is a system for defining and communicating geometric tolerances and features in technical drawings. It allows for clear and precise dimensioning of complex shapes, such as curves, circles, and irregular surfaces.
Significance of Dimensioning:
Accurate and consistent dimensioning is vital in engineering for the following reasons:
1. Manufacturability:
Dimensioning ensures that a part can be manufactured within the given tolerances and capabilities of the manufacturing process. It helps prevent errors, rework, and waste in production, ultimately contributing to cost-effective manufacturing.
2. Assembly and Interchangeability:
Proper dimensioning enables the correct assembly of parts, ensuring that they fit and function together as intended. Interchangeability of parts is also facilitated by adhering to dimensioning standards, allowing for convenient replacement and maintenance.
3. Communication and Collaboration:
Dimensioning serves as a language that engineers, designers, manufacturers, and other stakeholders in the product development process can understand and communicate effectively. It helps bridge the gap between design intent and realization.
Conclusion:
Dimensioning is an essential aspect of engineering design and manufacturing. It provides a standardized method for expressing the size, shape, and location of features on objects, ensuring accuracy, functionality, and interconnectivity of components. By following the principles and techniques of dimensioning, engineers can effectively communicate their design intent and facilitate the manufacturing and assembly processes.